“It is the great north wind that made the Vikings.” – Scandinavian Proverb
If the great north wind helped make the epic, strong Vikings, it’s no wonder that the wind impacts some of the recent innovations to create better, stronger construction practices! We’re seeing it happen day in and day out with new approaches for fenestration – windows and doors.
The Challenge
Homeowners increasingly want larger and larger expanses of glass in their homes. At the same time, municipalities, including Boulder, CO, have realized that due to climate change, wind speeds have increased. As a result, Building Departments have increased the required Design Pressure (DP) ratings for windows and doors. The DP rating represents a building component’s ability to withstand a given amount of wind load.
And the challenge is not simple because the wind loads vary based on numerous things including: is the component closer to the edge of a wall or higher up on the building – e.g. multi-story buildings. In short, wind loads are a bit of a moving target across the building facade.
Additional Challenges
With large glazing assemblies, often windows are mulled together creating hinge points which are weak points in the window assembly. Also, as the size of the assembly increases, the DP rating generally suffers – decreases. There are ways to increase the strength and DP rating of window assemblies which include adding structural mullions, thicker glass, and/or frame reinforcements. However, these methods help only so much and eventually additional approaches must be considered – especially since homeowners are increasingly requesting entire window walls. The question becomes … How do we create a window wall with high performance and well insulated assemblies without having to use generally lower performance, more costly, commercial focused, structural storefront, curtain wall and ribbon window technologies?
Consider Steel Tube, LVL or Lumber posts between the windows and doors
While we are not structural engineers here at AE Building Systems, we have been able to help our customers manage the new DP rating requirements necessary for code by suggesting solutions like leveraging steel tube, LVL, or lumber posts at the breaks in the window assemblies. You might think that it’s going to greatly reduce the performance due to thermal bridging and you’re right. Insulating those posts is critical.
Overview of the Steel Tube/LVL/Lumber Assembly:
Insulate Strategically
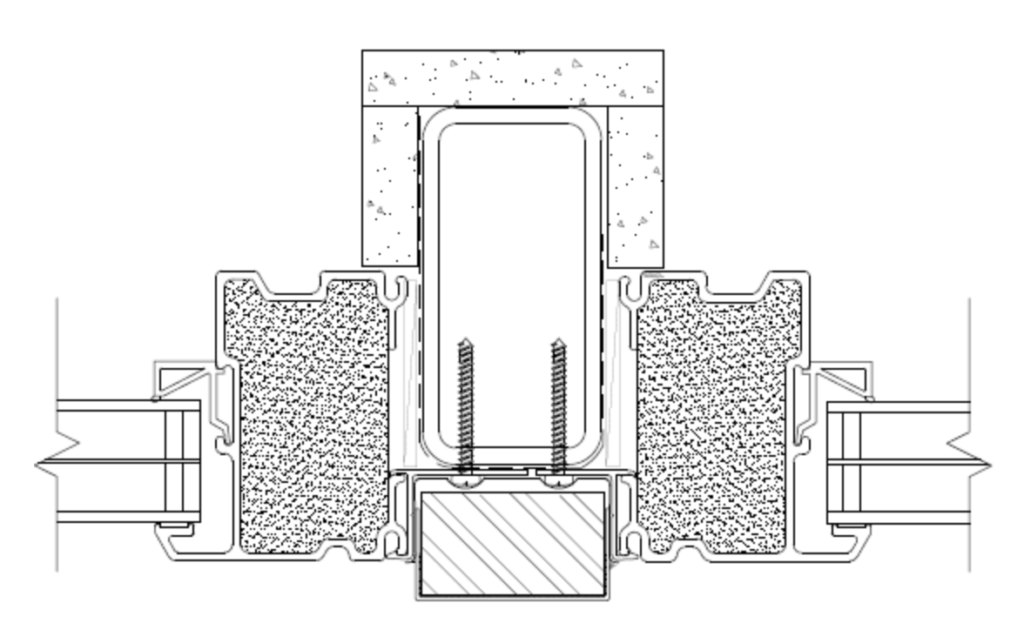
Good design that withstands higher wind loads is possible with this steel tube/LVL/Lumber window surround or vertical posts. In the assembly diagrammed below, double LVL’s are used and then insulated with a block of insulation. The insulation is then wrapped in break metal. While a double 2x could also be used, LVLs and steel tube are stronger and more dimensionally stable than say a double 2×4. The use of steel tube and LVL helps minimize the bulkiness/width of sight lines, and these are done on the vertical as vertical posts. Keep in mind that windows at the edge of walls or near corners typically have higher DP or wind-load requirements than those in the center of the wall. Also keep in mind that the width of the steel tube or LVL is an important consideration as ideally the window screw flange (often referred to as nail fin) doesn’t overlap.
Especially if you use the steel tube option, you will have significant thermal bridging, so it’s vital to insulate strategically. The image above shows a fairly small thermal break proud (to the bottom) of the LVLs. We would suggest a deeper block of insulation and then the brake metal wrap should be designed accordingly. Some builders have used fairly thick blocks of insulation outboard of the LVLs or steel tube – e.g. 3” of foam. As mentioned above, you generally do not want to overlap the screw flanges (nail fins). One option might include increasing the RO just enough to accommodate the flanges without overlapping them.
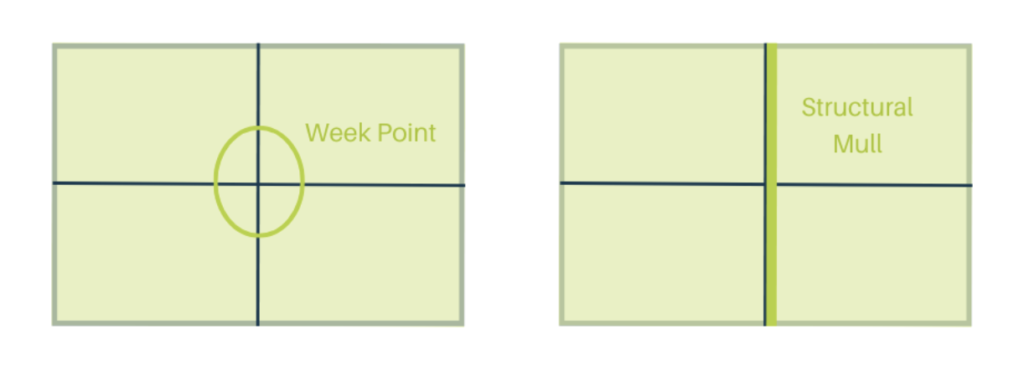
Benefits:
- Large assemblies or even “window walls” using this vertical post approach are possible and meet the wind-load requirements.
- Steel Tubes and LVLs can help reduce the bulkiness of vertical posts.
- Vertical posts can help reduce the required header size generally required for large expanses of glass.
- Allows for more design freedom to build creative elements into the design of the home, while still sticking within code parameters.
- Allows for smaller glazing assemblies which can more readily be transported without heavy equipment, reducing cost.
Cons:
- Requires insulation as the use of the steel tube or heavy lumber can be a significant source of energy loss. It is critical that the design includes an insulation component, and more is better.
- This assembly can be more costly and require more labor to build.
If you find yourself working on a project with tight constraints around wind-load parameters, consider an approach like this. Our team is more than happy to talk through how this works in real life and what considerations you may want to have as you design out this assembly!
Disclaimer: Please consult your structural engineer when using these concepts.