As 2024 winds down, we’ve been reflecting on a great year—and, true to form, diving into the data! We analyzed this year’s blog posts to uncover the “hottest high-performance topics of 2024.”
The big trend we discovered is that readers are eager to learn how to conserve energy, improve thermal performance, and cut costs at home. Innovations in window technology and reducing reliance on natural gas sparked particular interest, signaling that 2025 could be a great year for increased awareness of Passive House principles.
1. Goodbye Gas Line: How the Collins-Ruddy Residence Reduced Their Reliance on Natural Gas
Todd Collins and his family have been on a multi-phase journey to retrofit their home in Golden, Colorado, aiming to get as close to net zero as possible—all while maintaining a comfortable living environment.
In this article, we explored the latest step in their sustainability journey: replacing their water heater and furnace and capping their gas line. We dive into the details of their new water heater, what drove their decisions, how they approached the upgrade, and whether it’s delivering the results they hoped for.
Todd practices what he preaches about embracing Passive House principles, and his family’s decision to make this change came down to several key factors:
- Achieve their goal of net zero energy and reduce fossil fuel use
- Eliminate environmental and safety risks (no gas = no carbon monoxide danger)
- Lower utility costs by relying more on solar power
- Taking advantage of timing, as the old water heater was due for replacement
- Relocate the water heater to a more efficient spot in the home for better thermal performance.
The result was a resounding success! Their family of four, including two teenagers, has seamlessly transitioned to the new system. This upgrade has improved their home’s energy efficiency while enhancing their quality of life and peace of mind.Curious about the products Todd used and how he made it all happen? Check out the full story of how the Collins-Ruddy residence capped their gas line and took another step toward sustainability.
2. Alpen Climbing Higher With Two Big Announcements
This year, Alpen High Performance Products made headlines with two major announcements: a $5.8 million grant from the U.S. Department of Energy (DOE) and the appointment of Andrew Zech as their new CEO. These milestones mark an exciting period of growth and innovation for the company.
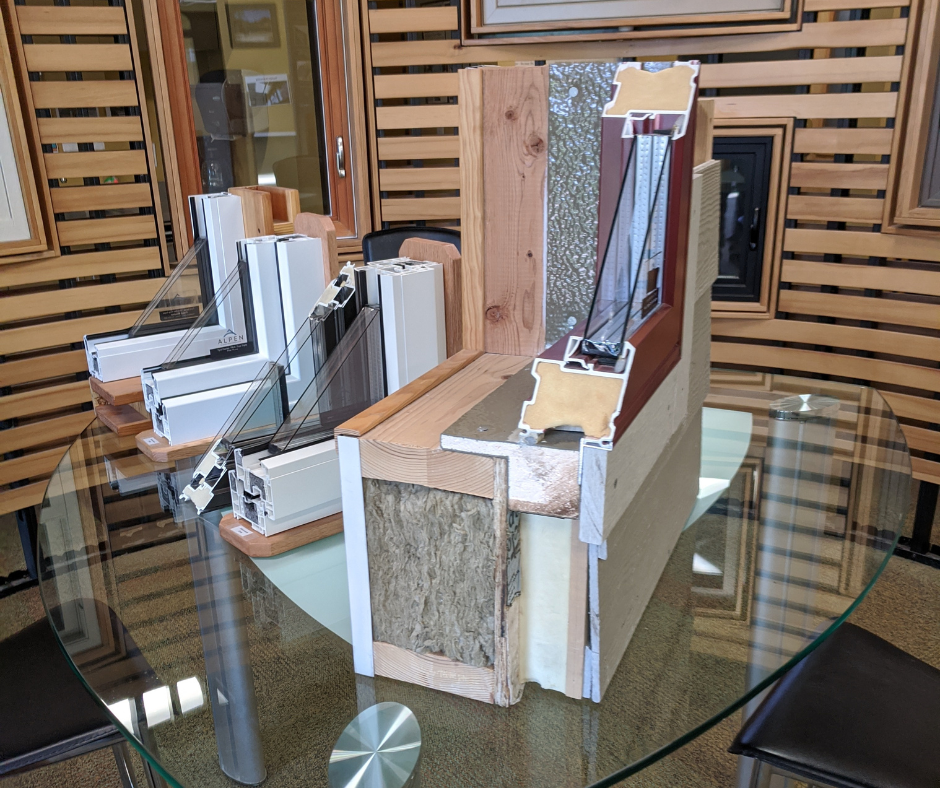
Here’s what these updates mean for Alpen:
- Well-earned recognition for their dedication to designing high-performance windows and doors that enhance energy efficiency and sustainability.
- Creation of over 100 new jobs thanks to DOE funding
- Expansion with a new manufacturing facility in Vandergrift, PA
- A projected tenfold increase in production capacity to meet the growing demand for products that improve thermal performance.
AE has proudly worked with Alpen for over a decade, and we’re thrilled to see their continued success. Read more about Alpen’s success and AE’s collaborations with the window manufacturer.
3. High-Performing Windows for High-Performing Homes
Rounding out our top three blog posts of 2024, Alpen High Performance Products continues to rack up accolades—and the results mean even more savings for consumers.
This year, Alpen’s Zenith line of high-performance windows earned a spot on EnergyStar’s prestigious “Most Efficient” rating scale. While Passiv Haus standards are even more rigorous, this recognition highlights Alpen’s commitment to sustainability and efficiency. Their windows also featured prominently in multiple award-winning projects showcased at the PHIUS Passive House Conference.
What this means for consumers:
- Up to $600 in federal tax credits for qualifying windows and doors through 2032
- EnergyStar upgrade assistance options
- High-performance products that deliver real energy savings
Want to learn how Alpen products can help you save money and energy? Get all the details here.
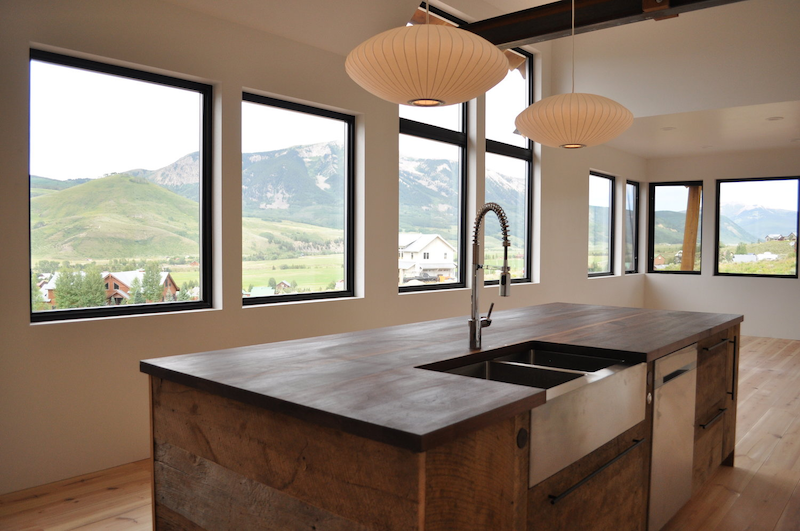
We’re excited to see what our readers are eager to explore in the year ahead. Don’t miss a single update on Passiv Haus and high-performance construction—subscribe to our newsletter and start 2025 informed and inspired.
Wishing a Happy New Year to all our clients, colleagues, and friends in the industry!